E' opportuno approfondire i tre punti seguenti prima di procedere all'acquisto di una saldatrice:
In caso la saldatrice venga alimentata da un generatore di corrente è consigliabile utilizzarne uno stabilizzato che possa erogare una potenza sensibilmente superiore a quella richiesta dalla saldatrice durante la specifica applicazione, indicativamente si considera un fattore 1,5: ad esempio, per saldare a 100A con un inverter per elettrodo occorrono circa 2,5kW, quindi il generatore dovrà essere in grado di fornire almeno 2,5×1,5 = 3,75 kW. Questa precauzione evita problemi in fase di innesco dell’arco elettrico, quando è osservabile un picco di assorbimento da parte della saldatrice. Si consiglia inoltre di scegliere una saldatrice progettata per l’allacciamento ai generatori, con una tolleranza nei confronti delle variazioni della tensione di alimentazione superiore al 10% (minima prevista dalla normativa di prodotto): in commercio esistono saldatrici con alimentazione 230V +/-30%, che significa tollerare sbalzi di tensione di +/-69V in ingresso senza danni per l’inverter.
Anche l’uso delle prolunghe deve essere fatto con attenzione: allungare il cavo di alimentazione della saldatrice significa introdurre una caduta di tensione, quella sul cavo, prima dell’ingresso della macchina, e se questa caduta è superiore alla tolleranza che l’inverter può sopportare si verifica un malfunzionamento. Se è necessario utilizzare una prolunga, è consigliabile sceglierne una con sezione pari a quella del cavo di alimentazione della saldatrice (maggiore è la sezione del cavo, minore è la caduta di tensione).
Diminuendo la corrente di saldatura impostata il duty cycle aumenta ed aumenta anche, a parità di corrente, se la temperatura ambiente diminuisce, perché la macchina si riscalda più lentamente.
Una volta individuati il materiale da saldare, le condizioni operative ed il ciclo di lavoro necessario, si può decidere quale processo di saldatura è il più adatto tra i seguenti:
- Saldatura ad elettrodo – MMA (Manual Metal Arc)
- Saldatura a filo – MIG/MAG (Metal Inert Gas / Metal Active Gas)
- Saldatura TIG (Tungsten Inert Gas)
Saldatura ad elettrodo MMA
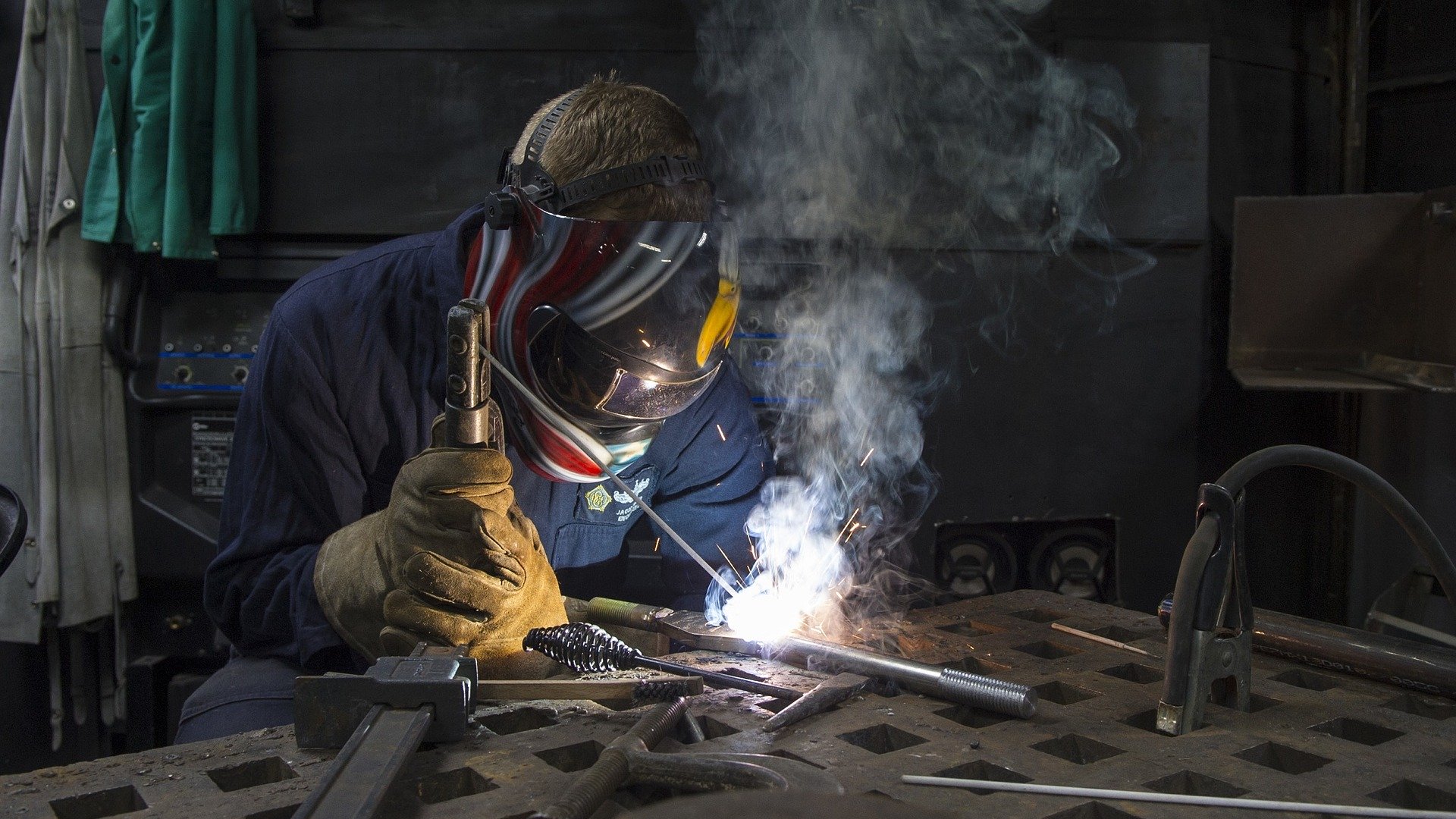
La saldatura ad arco metallico manuale (MMA) o saldatura ad elettrodo sfrutta il calore dell’arco elettrico che si genera tra l’elettrodo ed il pezzo da saldare.
E’ la tecnica di saldatura più diffusa al mondo grazie alla semplicità dell’impianto che non richiede l’utilizzo del gas di protezione. L’elettrodo è costituito da un’anima metallica e da un rivestimento. L’anima può avere diametri e lunghezze diversi e deve corrispondere al materiale da saldare. Il rivestimento svolge la funzione principale di protezione del bagno di saldatura dai contaminanti presenti nell’aria, funzione svolta dal gas negli altri processi di saldatura, inoltre può apportare degli elementi di lega e pulire il bagno di fusione.
Con questo procedimento si salda comunemente il ferro e l’acciaio inox. Si possono effettuare piccole riparazioni di oggetti in ghisa. La saldatura dell’alluminio, anche se possibile con elettrodo alluminio e macchina speciale, risulta difficile e con risultati estetici poco soddisfacenti. Per altri metalli la saldatura ad elettrodo è sconsigliata o addirittura impossibile. Per ogni tipo di elettrodo vanno seguite le indicazioni riportate sulla confezione relative alla polarità (connessione al polo positivo o negativo della saldatrice) ed intensità di corrente.
Alcune saldatrici per elettrodo ancora reperibili in commercio, di vecchia progettazione, erogano corrente di polarità alternata e non continua: con queste è possibile saldare agevolmente soltanto gli elettrodi rutili. Laboratorio Saldatura propone soltanto saldatrici MMA moderne che erogano corrente continua.
Il procedimento di saldatura ad elettrodo permette di operare in tutte le posizioni (il giunto di saldatura può essere orizzontale, verticale, sopra-testa), a patto di scegliere l’elettrodo corretto, disporre della saldatrice idonea ed avere esperienza. E’ possibile saldare in ambiente chiuso oppure all’aperto (non c’è il problema del gas di protezione che all’esterno può essere tolto dal vento).
La pinza porta-elettrodo impugnata dall’operatore risulta sempre maneggevole, perché pesa poco e perché il cavo di saldatura connesso è un semplice cavo elettrico rivestito in gomma, senza trasporto di gas e liquidi. L’impianto complessivo è costituito dalla saldatrice (se si tratta di un inverter è piccola e leggera), e i due cavi di saldatura e massa in uscita, pertanto risulta facilmente trasportabile ovunque.
Lo svantaggio di questa tecnica di saldatura è la produttività limitata: si deve fare una pausa ogni volta che l’elettrodo è consumato (un elettrodo rutile 2,5x300mm brucia in un minuto circa di saldatura continua) per sostituirlo con uno nuovo ed occorre rimuovere la scoria protettiva lasciata in superficie a seguito della fusione del rivestimento.
Gli elettrodi possono essere divisi in tre gruppi principali:
- Rutili
- Basici
- Cellulosici
Gli elettrodi rutili contengono un’alta percentuale di ossido di titanio (rutilo) nel rivestimento. L’ossido di titanio permette una facile accensione dell’arco, uno scorrimento regolare e poche proiezioni di metallo fuso. I rutili sono elettrodi per uso generale con buone proprietà di saldatura ed ottimo risultato estetico. Hanno un basso costo e sono largamente impiegati per tutte le applicazioni comuni su acciaio, risultando gli elettrodi più diffusi nel mercato. Possono essere saldati in corrente alternata AC o in corrente continua DC collegati al polo negativo della saldatrice, modalità che prende il nome di polarità diretta.
Gli elettrodi basici contengono un’alta percentuale di carbonato di calcio (calcare) e fluoruro di calcio (fluorite) nel rivestimento. La fluorite ostacola la stabilità dell’arco pertanto devono essere saldati con saldatrici che consentono buona lunghezza d’arco elettrico, in corrente continua DC collegati al polo positivo della saldatrice, modalità che prende il nome di polarità inversa. I basici richiedono correnti più elevate rispetto ai rutili a parità di diametro, l’arco è più difficile da innescare e mantenere acceso, la rimozione della scoria è più difficile. Vengono utilizzati da operatori esperti per la saldatura di strutture di carpenteria media e pesante per la quale sono richieste qualità di saldatura professionale, elevate proprietà meccaniche dei giunti saldati e resistenza alle rotture garantita.
Gli elettrodi cellulosici contengono un’alta percentuale di cellulosa nel rivestimento. Per l’innesco e la saldatura è necessario disporre di una macchina con elevata tensione a vuoto e preferibilmente regolazione dell’ARC-FORCE, un parametro che permette di ridurre gli spegnimenti dell’arco elettrico . Consentono un’elevata penetrazione del bagno fuso, caratteristica che li rende molto indicati per l’unione di tubi, perché è un’applicazione che non permette la verifica del cordone a rovescio e pertanto si rende necessaria la garanzia di una buona profondità di fusione.
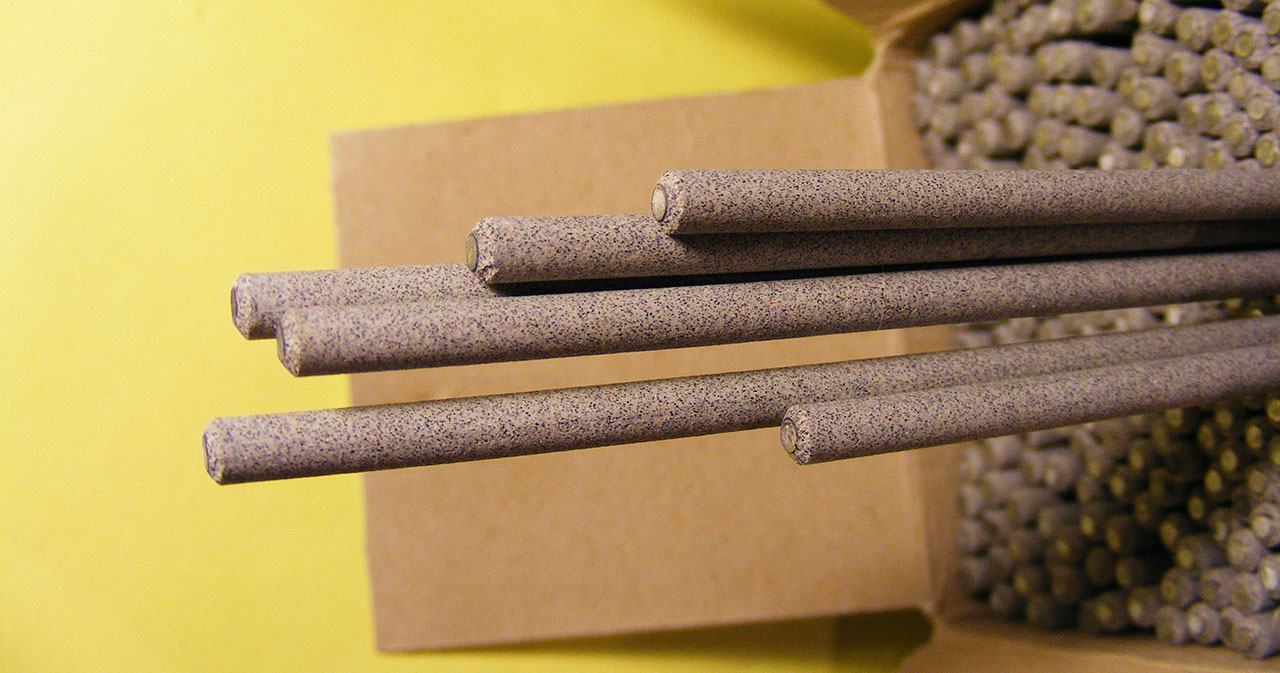
Opzioni, parametri e controlli comunemente usati
Vantaggi
- Saldature in qualunque posizione, all’interno ed all’aperto.
- Maneggevolezza del porta-elettrodo, semplicità dell’impianto (no gas, no liquidi raffreddamento).
Svantaggi
- Bassa produttività: è necessario fermarsi ad ogni cambio dell’elettrodo, deve essere rimossa la scoria.
- Richiede molta esperienza e buona manualità.
SUGGERIMENTI PRATICI
- L’anima dell’elettrodo deve essere di materiale compatibile con quello da saldare (ferro con ferro, inox con inox, ghisa con ghisa …); con il termine “ferro” si indica comunemente l’acciaio NON inossidabile
- Il diametro dell’elettrodo rappresenta il limite inferiore dello spessore saldabile: è difficile saldare una lamiera spessa 2,0mm con un elettrodo di diametro 3,2mm senza “sfondare”
- Il rivestimento dell’elettrodo ha funzioni precise, il rutile è adatto ad impieghi generici di manutenzione, il basico si usa se è richiesta una tenuta più sicura del giunto, il cellulosico ha molta penetrazione e si usa se la saldatura non può essere controllata a rovescio (es: tubi)
- Rispettare le indicazioni di polarità e corrente riportate dal costruttore sulla confezione degli elettrodi
- Verificare che l’elettrodo sia compatibile con la saldatrice di cui si dispone, in termini di corrente massima erogabile e tensione d’arco: tutte le saldatrici saldano i rutili, non tutte saldano i basici, poche saldano i cellulosici
- Gli elettrodi per alluminio richiedono particolari caratteristiche d’arco elettrico e quindi saldatrici specifiche: spesso risultano idonee quelle indicate per elettrodi cellulosici (elevata tensione a vuoto)
- Verificare che la potenza elettrica disponibile sia sufficiente in relazione all’elettrodo scelto: maggiore è il diametro dell’elettrodo, maggiore è la potenza richiesta; in generale per uso domestico (3kW) è preferibile non superare il diametro 2,5mm
- Una saldatrice con alimentazione richiesta 230V 1ph che assorbe 6kW regolata alla massima corrente, può comunque essere collegata ad una presa domestica 3kW se regolata ad una corrente inferiore; ad esempio alla corrente richiesta da un elettrodo rutile 2,5mm l’assorbimento della saldatrice è in genere compreso tra 2 e 2,5kW
- Pulire accuratamente i pezzi da saldare rimuovendo polvere, grasso, residui di vernice e ruggine; il punto di fusione di queste impurità è diverso da quello del materiale base e per questo motivo durante la solidificazione possono formarsi dei crateri e delle crepe (cricche a caldo)
- Rimuovere l’umidità dai pezzi da saldare asciugandoli ed eventualmente pre-riscaldandoli a seconda dello spessore e del materiale; la rimozione dell’umidità evita diffusione di idrogeno e rischio di cricche a freddo (anche molte ore dopo la solidificazione del giunto); il pre-riscaldo rallenta la solidificazione ed evita tensioni eccessive del metallo in seguito ai fenomeni di ritiro
- Usare elettrodi ben conservati ed asciutti, eventualmente asciugarli in un fornetto apposito o usare un forno generico a temperatura attorno a 50°C, allo scopo di eliminare l’umidità
- Regolare la corrente in modo opportuno in modo che la saldatura risulti ben penetrata senza sfondamenti (troppa corrente, cordone troppo concavo) o fenomeni di incollatura superficiale del materiale d’apporto al pezzo senza tenuta meccanica (poca corrente, cordone troppo convesso)
- Muovere l’elettrodo con tecnica a tirare, mantenendo un’angolazione dello stesso di circa 45° rispetto al cordone e procedere nel verso di quell’angolo; in questo modo si evita il rischio di includere scoria all’interno del bagno di saldatura (con rischio di fragilità della giunzione e rottura)
Saldatrice Professionale Inverter MMA per tutti i tipi di elettrodo, incluso cellulosico e alluminio.
Saldatura a filo continuo MIG/MAG
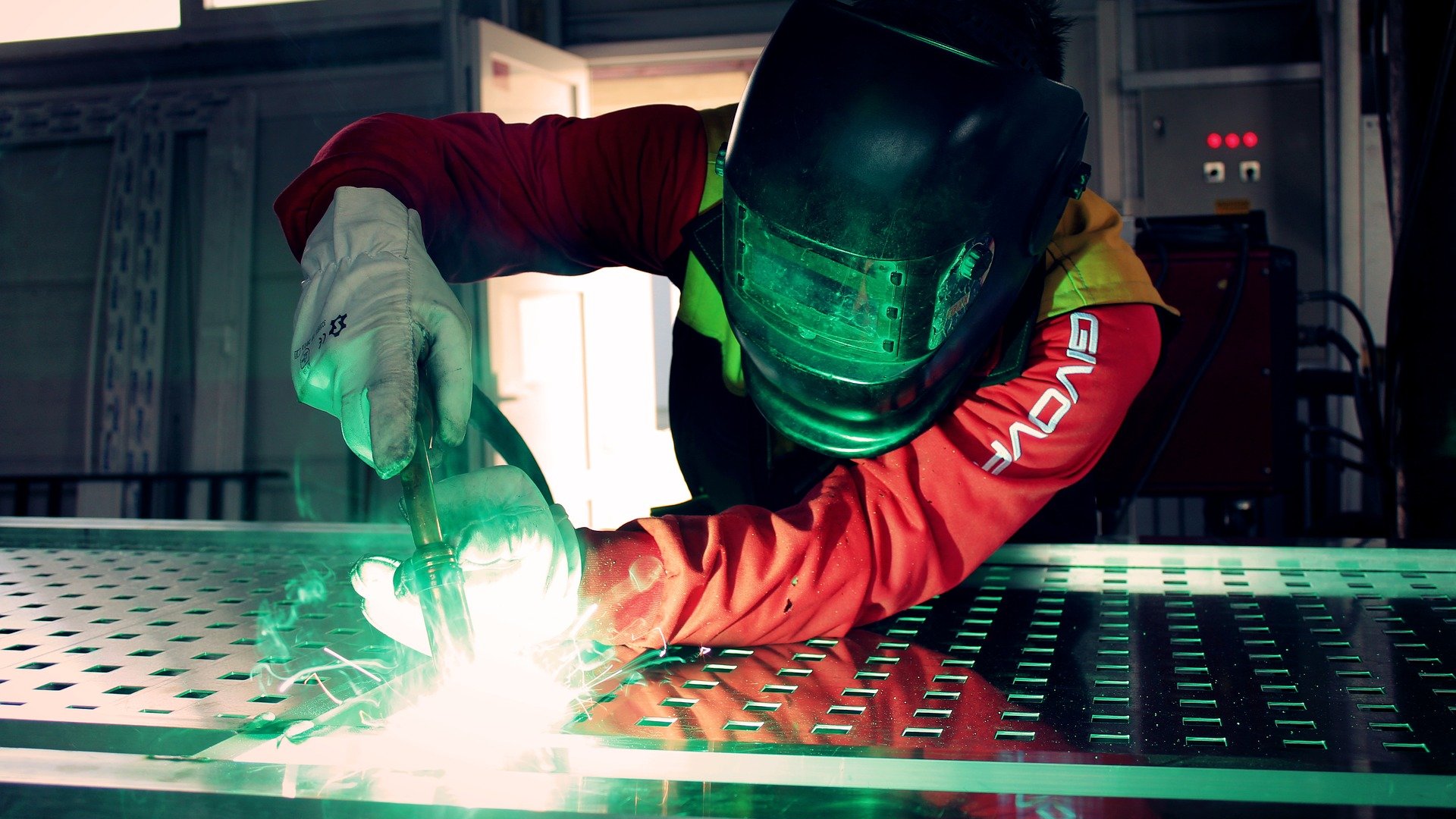
La saldatura MIG/MAG sfrutta il calore dell’arco elettrico che si genera tra il pezzo da saldare ed un filo elettrodo fusibile che costituisce il materiale d’apporto.
Il filo viene alimentato di continuo verso il cordone per mezzo di una TORCIA connessa elettricamente alla saldatrice attraverso un UGELLO PORTA-CORRENTE che conduce per contatto la corrente di saldatura al filo stesso. Il filo è avvolto in BOBINE disponibili commercialmente in varie dimensioni e formati, i più comuni sono:
- Bobina diametro 100 mm con circa 1 kg di filo
- Bobina diametro 200 mm con 5 kg di filo
- Bobina diametro 300 mm con 15 kg di filo
Il trascinamento del filo attraverso la torcia fino all’ugello porta-corrente è realizzato da un dispositivo montato sulla saldatrice che prende il nome di TRAINAFILO, un assieme elettromeccanico formato da un motore elettrico e da un meccanismo di ingranaggi e RULLI che stringono il filo e lo producano dalla bobina all’ingresso della torcia. Le saldatrici per uso domestico o per impieghi professionali non gravosi hanno in genere un traino a 2 rulli, idoneo per bobine fino a 5kg. Gli impianti per uso industriale in carpenteria pesante hanno preferibilmente un sistema a 4 rulli, consigliato per le bobine da 15kg. La forza con cui i rulli stringono il filo è regolabile tramite appositi bracci di pressione e deve essere non troppa, perché se il filo tocca il pezzo e non può avanzare i rulli devono slittare (altrimenti il filo si aggroviglia in entrata della torcia), né troppo poca, altrimenti il trascinamento del filo non è regolare. E’ molto importante seguire con attenzione le indicazioni del costruttore per quanto riguarda la messa a punto della saldatrice in relazione al trascinamento del filo, ricordando che per ogni tipo filo (occorre conoscere materiale e diametro) devono essere montati gli accessori idonei, in particolare:
- rullo trainafilo
- guaina di scorrimento del filo all’interno del cavo torcia
- ugello porta-corrente
Il filo di saldatura è normalmente un filo di metallo pieno, corrispondente al materiale da saldare. Esistono dei fili chiamati animati o tubolari che all’interno contengono delle miscele di elementi (flussi) per aggiungere qualità meccanica alla saldatura. Il filo pieno non genera scoria superficiale, mentre il filo animato genera una scoria come quella dell’elettrodo (il flusso è fatto degli stessi elementi usati per i rivestimenti) che deve essere rimossa utilizzando spazzola e martellina. Un cenno a parte merita un particolare filo animato che può essere utilizzato senza protezione gassosa: in gergo tecnico ci si riferisce a questo col nome di filo animato NO-GAS. Questo filo è molto utilizzato in ambito domestico fai-da-te, per saldatura di acciaio comune, perché evita all’utilizzatore l’acquisto della bombola di gas e consente comunque i vantaggi di velocità e semplicità esecutive tipiche della saldatura a filo.
La saldatura a filo avviene con polarità inversa, con la torcia collegata al polo positivo della saldatrice. Fa eccezione il filo animato NO-GAS, per il quale la polarità deve essere diretta. Le macchine che consentono l’uso di filo MIG/MAG ed anche NO-GAS devono prevedere l’inversione di polarità della torcia.
La saldatura MIG/MAG è una tecnica molto versatile idonea per spessori sottili o grandi e si impiega comunemente per la saldatura di:
- Ferro ed altri acciai non legati
- Acciai legati ed inossidabili
- Alluminio e sue leghe
Questo procedimento supera il limite applicativo della saldatura MMA costituito dal cambio dell’elettrodo, inoltre risulta più semplice da gestire per l’operatore, perché ci si deve preoccupare soltanto di procedere con la torcia lungo i lembi da saldare ma non di avvicinare progressivamente la mano al bagno di saldatura, azione necessaria con la tecnica ad elettrodo. Anche l’innesco è molto più semplice, perché l’elettrodo, in particolare se appena sostituito, costringe ad un’impugnatura molto distante dal pezzo da saldare ed ogni piccolo movimento della mano risulta amplificato.
La fusione del filo genera il distacco di gocce di metallo fuso che si trasferiscono nel bagno di saldatura; al variare della corrente, cambia anche la dimensione delle gocce e del numero di gocce che si staccano nell’unità di tempo, di conseguenza la modalità di trasferimento del metallo assume nomi diversi:
- Trasferimento ad immersione – SHORT ARC
Il trasferimento ad immersione è indicato per spessori di lavoro sottili, il metallo fuso che si forma all’estremità del filo viene trasferito per immersione nel bagno di saldatura, si crea un ponte liquido tra il filo stesso ed il metallo da saldare. Il processo avviene ad una bassa tensione media d’arco elettrico. La cura nell’impostazione della tensione della saldatrice, della velocità di avanzamento del filo e dell’induttanza di uscita è essenziale per stabilizzare l’arco e ridurre al minimo le proiezioni di metallo fuso. L’induttanza ha la funzione di controllare il picco di corrente che si verifica quando il filo si immerge nel bagno di saldatura. Nelle moderne saldatrici inverter sinergiche questi parametri sono impostati automaticamente al momento della selezione del tipo e spessore di materiale da saldare, gas impiegato e caratteristiche del filo impiegato.
- Trasferimento a spruzzo – SPRAY ARC
Il trasferimento a spruzzo è indicato per spessori di lavoro non sottili quando è necessario un alto tasso di deposito di metallo d’apporto. Le gocce di metallo fuso sono piccole e l’arco risulta stabile e ben gestibile, con assenza di proiezioni importanti. E’ necessaria un’elevata energia in termini di tensione e corrente di saldatura, al di sotto della quale questo processo non può avere luogo.
Nell’intervallo di corrente compreso tra i valori del trasferimento SHORT ARC e quello SPRAY ARC, il trasferimento avviene in modo disordinato, l’energia dell’arco non è sufficiente per impedire la formazione di gocce grandi all’estremità del filo: è il regime globulare (DROP ARC), una modalità che si cerca di evitare, perché l’arco elettrico risulta difficile da gestire e si osservano numerose ed indesiderate proiezioni di metallo fuso provocate dalle gocce che cadono in modo disordinato nel bagno di saldatura.
- Trasferimento pulsato – PULSED ARC
Il trasferimento pulsato è stato sviluppato per stabilizzare l’arco a livelli di corrente inferiori alla soglia dello SPRAY ARC, evitando i cortocircuiti e le proiezioni tipiche del regime globulare. Il trasferimento del metallo è regolato da impulsi di corrente, ogni impulso ha un’energia sufficiente per staccare una goccia. In questo modo si ottiene una gestione precisa della saldatura, modulando apporto di materiale e di calore. La possibilità di dosare l’apporto di calore risulta molto utile quando si saldano metalli ad alta conduttività termica (es. alluminio) per evitare sfondamenti e deformazioni. Si può agire sulla frequenza delle pulsazioni per ottenere la sequenza di gocce desiderata per un ottimo risultato estetico (saldature a vista).
Opzioni, parametri e controlli comunemente usati
Vantaggi
- Maggiore produttività rispetto al processo MMA, non si deve cambiare l’elettrodo consumato ed il filo pieno non richiede la rimozione della scoria.
- Facilità d’uso per utilizzatori non esperti, buona visibilità del bagno di fusione.
- Indicato sia per spessori alti che sottili.
- Saldatura più agevole di inox e alluminio.
Svantaggi
- Maggior costo della saldatrice rispetto all’elettrodo, apparecchiatura complessa.
- Manutenzione della torcia, reperimento gas.
- Difficile saldare all’esterno, il vento porta via la protezione gassosa (è possibile con filo NO-GAS, ma solo su acciaio comune).
- La regolazione contemporanea della tensione d’arco e della velocità di alimentazione del filo richiede esperienza se non si dispone di una moderna saldatrice sinergica.
SUGGERIMENTI PRATICI
- Verificare di avere a disposizione tutto il necessario per eseguire la saldatura, in particolare filo e gas adeguati per il materiale di lavoro
- Controllare che il rullino traina-filo sia idoneo per diametro e tipologia della gola; la gola a V è per l’acciaio, la gola a U per l’alluminio e quella zigrinata per il filo tubolare (animato); in genere i rullini sono identificati anche con una sigla esplicativa; in caso si disponga del solo rullino per acciaio e lo si usi per alluminio, è opportuno regolare i braccetti di pressione allentandoli di un giro o due (questo accorgimento è valido anche per il filo tubolare)
- Controllare che la guaina e la punta guida-filo montate sulla torcia siano idonee al filo utilizzato relativamente a diametro e tipo di materiale: filo acciaio e filo tubolare si saldano con la stessa guaina e la stessa punta, filo alluminio si salda con guaina teflon o grafite e con punta dedicata
- Cambiare il rullino traina-filo ed usare un rullino specifico con la gola tonda ad “U”; se non disponibile usare il rullino per filo acciaio del diametro richiesto ed allentare di un giro il braccetto di pressione del traina-filo
- Sostituire la guaina della torcia con una specifica per filo alluminio, in teflon o grafite; la guaina deve sporgere dalla spina EURO della torcia ed entrare nella presa EURO della saldatrice (rimuovere la cannetta in ottone che si usa per il filo acciaio/animato) fino ad arrivare in prossimità del rullino di trascinamento, in questo modo il filo alluminio è guidato in modo ottimale e si evita il rischio di grovigli prima dell’ingresso in torcia
- Usare una punta guidafilo specifica per alluminio; questa ha un foro leggermente maggiorato rispetto alla punta del corrispondente diametro per acciaio; in alternativa provare una punta per acciaio del diametro immediatamente superiore a quello del filo alluminio usato
- Usare Argon puro come gas di protezione
- L’alluminio ha una conducibilità termica elevata, bisogna prestare attenzione agli sfondamenti in caso di spessori sottili; in caso di spessori più importanti risulta spesso opportuno pre-riscaldare i pezzi per favorire la penetrazione; l’uso della corrente pulsata migliora notevolmente il risultato della saldatura
Saldatrice inverter 195A multiprocesso per saldatura a filo continuo MIG/MAG, filo senza GAS e ad elettrodo MMA, con accessori MMA e torcia a filo.
Saldatura TIG
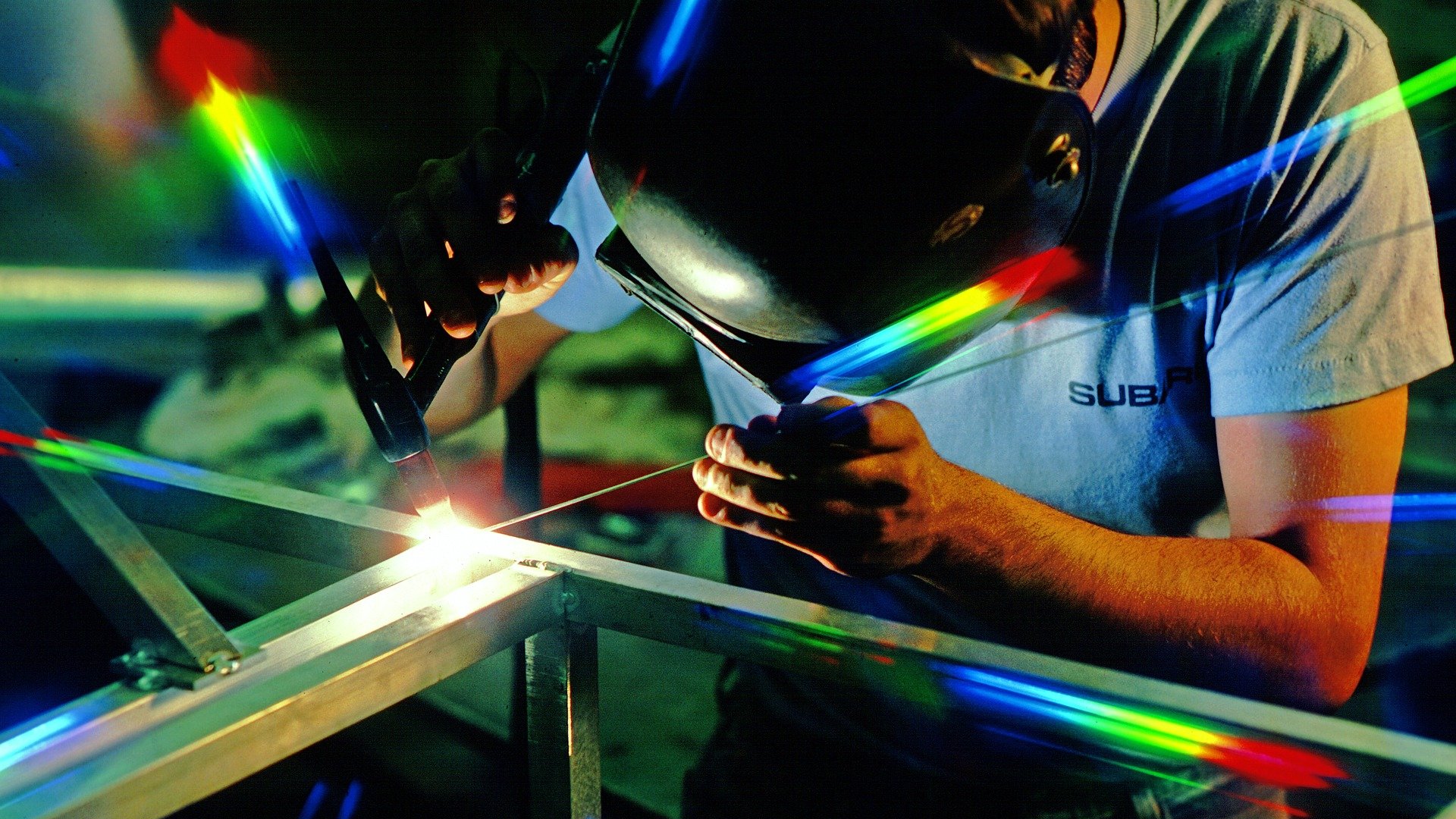
Il processo di saldatura TIG sfrutta il calore dell’arco elettrico che si forma tra un elettrodo di tungsteno infusibile alla temperatura d’esercizio e il pezzo in lavorazione, sotto la protezione di un gas inerte, comunemente Argon o miscele di Argon ed Elio. L’arco che si genera è intenso e preciso, ideale per saldature di alta qualità meccanica ed elevata precisione. Poiché l’elettrodo non viene consumato durante la saldatura, quando è richiesto materiale d’apporto, deve essere aggiunto tramite apposita bacchetta, chiamata appunto bacchetta TIG, in materiale corrispondente al metallo da saldare.
Il gas di protezione viene selezionato in base al materiale.
Argon puro è il gas di protezione più comunemente usato perché può essere utilizzato per una gamma ampia di materiali tra cui acciaio, acciaio inossidabile, alluminio e titanio.
Argon + Idrogeno (dal 2% al 5%) favorisce la realizzazione di saldature dall’aspetto più pulito senza ossidazione superficiale. L’arco risulta più caldo e più stretto ed è possibile aumentare la velocità esecutiva.
Elio puro o mix Argon/Elio aumentano la temperatura dell’arco favorendo una penetrazione più profonda.
Il processo TIG può essere impiegato per la saldatura di tutti i metalli, in particolare:
Alluminio e sue leghe, inox, rame, ottone, bronzo, titanio, nichel, leghe al magnesio.
L’arco di saldatura TIG può essere innescato in tre modi differenti:
A STRISCIO: si graffia la superficie del pezzo con l’elettrodo in tungsteno formando un cortocircuito, quando si interrompe il cortocircuito si avvia la corrente di saldatura principale. Questo innesco è poco preciso ed il contatto tra il pezzo e l’elettrodo provoca inclusioni di tungsteno nel bagno di saldatura, peggiorando le caratteristiche meccaniche del giunto.
INNESCO LIFT: il cortocircuito si forma a un livello di corrente molto basso appoggiando l’elettrodo al pezzo e sollevandolo lentamente. Questo tipo di innesco minimizza il rischio di contaminazione da tungsteno.
INNESCO HF: non c’è contatto tra elettrodo e pezzo, l’arco elettrico si avvia grazie ad un dispositivo chiamato in gergo tecnico ALTA FREQUENZA (HF = High Frequency). L’HF è costituita da un treno di scintille ad alta tensione (migliaia di volt) della durata di pochi microsecondi. Le scintille HF causano la ionizzazione dell’atmosfera gassosa tra elettrodo e pezzo da saldare innescando il passaggio di corrente tra i due diversi potenziali elettrici.
La saldatura TIG può avvenire con corrente continua DC (= Direct Current) oppure con corrente alternata AC (= Alternating Current).
Nella saldatura TIG AC la polarità della corrente è alternata, il generatore alterna i poli in uscita con frequenza opportuna. Si usa per l’alluminio e per le leghe al magnesio. Quando la polarità dell’elettrodo è negativa gli elettroni si muovono dal tungsteno verso il pezzo da saldare con apporto termico elevato: è la normale fase TIG di fusione. Nella fase in cui l’elettrodo ha polarità positiva gli elettroni escono dal pezzo da saldare e vanno verso la punta del tungsteno, rimuovendo lo strato di ossido superficiale tipico dell’alluminio: è la fase di pulizia o decapaggio. L’ossido superficiale, essendo isolante, rappresenta un ostacolo per il passaggio della corrente e pertanto la sua rimozione è necessaria per eseguire con successo la fase successiva di fusione che consente la saldatura.
Nella saldatura TIG DC la polarità della corrente di saldatura è continua. L’elettrodo ha sempre polarità negativa, la fase di fusione è continua. Si usa per tutti i metalli tranne l’alluminio e le leghe al magnesio.
Gli elettrodi più utilizzati sono quelli in tungsteno puro per la saldatura di alluminio e leghe al magnesio in TIG AC e quelli in tungsteno/cerio 2% per la saldatura di acciaio ed inox in TIG DC.
Opzioni, parametri e controlli comunemente usati
La corrente passa di continuo dal valore impostato (= corrente di picco) a un valore ridotto (= corrente di base) e viceversa. Si usa per dosare l’apporto termico al pezzo da saldare, per regolare la penetrazione nella saldatura ed evitare crateri e sfondamenti.
Vantaggi
- Ottima qualità del giunto saldato e aspetto estetico del cordone.
- Adatto per la realizzazione di saldature di precisione e per spessori sottili.
Svantaggi
- L’aggiunta di materiale d’apporto attraverso la bacchetta TIG richiede buona manualità.
- Bassa produttività.
- Apparecchiatura complessa e costosa.
Saldatrice inverter pulsata 200A per saldatura TIG DC e AC (alluminio) con innesco HF, con accessori MMA, torcia TIG e ricambi.
Taglio PLASMA
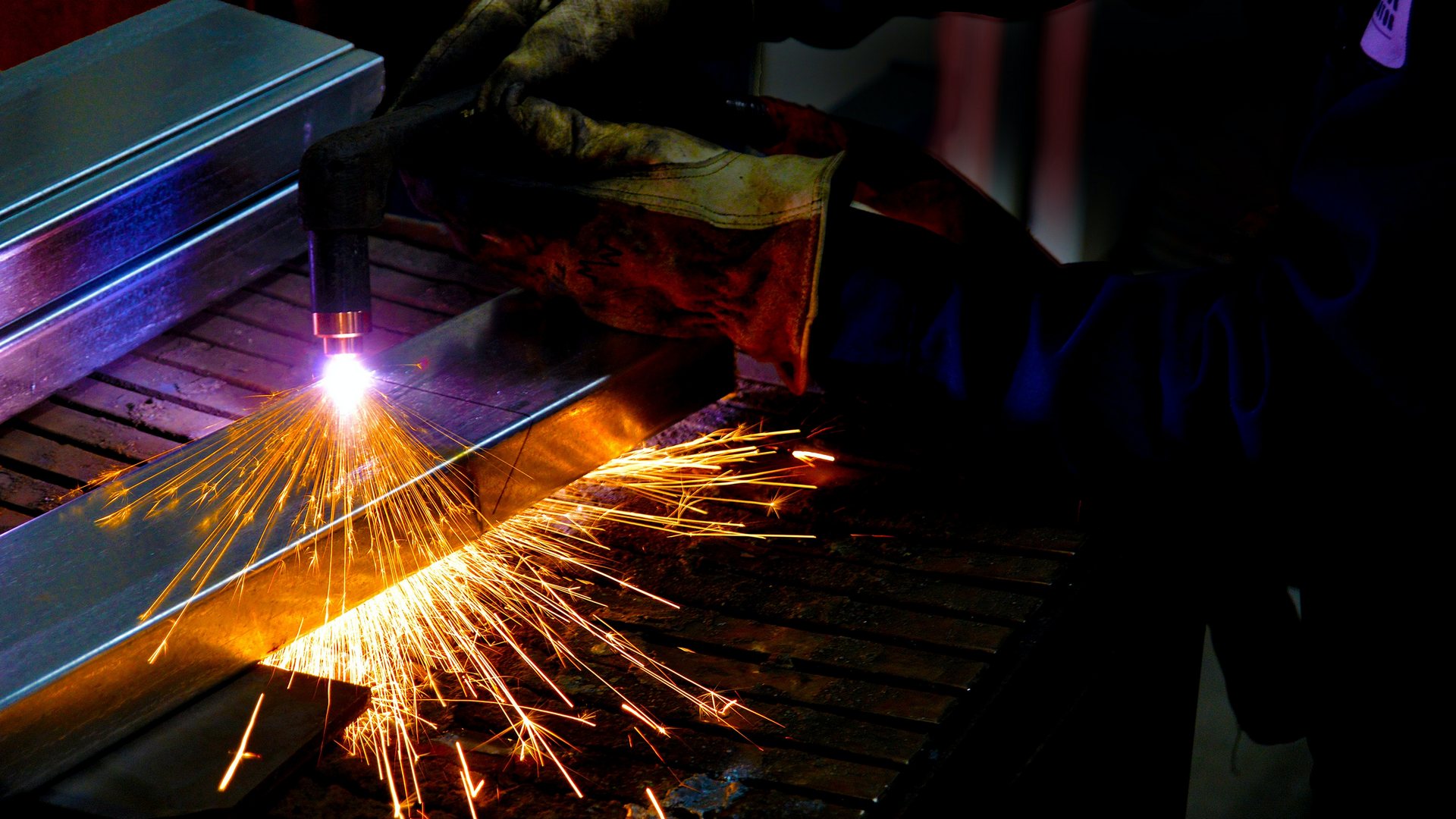
Il plasma è un gas fortemente ionizzato, ovvero composto da particelle cariche, e quindi conduttore di corrente elettrica. Esso può essere ottenuto facendo passare il gas da ionizzare, in genere aria compressa o gas inerte, attraverso un arco elettrico generato all’interno di una strozzatura meccanica. In questo modo la concentrazione delle particelle cariche che si formano aumenta notevolmente, di conseguenza aumenta l’effetto termico e si innalza la temperatura. Il gas ad alta temperatura tende ad espandersi e, attraversando la strozzatura, acquisisce una velocità molto elevata: si ottiene un dardo di cariche ad energia concentrata, utilizzabile per tagliare i metalli.
Si può realizzare un impianto di taglio al plasma utilizzando un generatore di corrente con caratteristiche opportune, una sorgente di gas ed una torcia che convoglia il gas in un ugello al cui interno viene generato l’arco elettrico.
In caso si utilizzi semplicemente aria compressa, è sufficiente un compressore, che può essere integrato nel generatore o separato. E’ consigliabile usare dei filtri per rimuovere la condensa dall’aria, la quale potrebbe provocare danni alla torcia.
E’ comunque fondamentale la manutenzione delle parti consumabili della torcia, in dettaglio:
Opzioni, parametri e controlli comunemente usati